Case Study Overview
Objective
Explore the importance of quality management within a manufacturing context, particularly in furniture production. Students will analyze a real-world scenario to identify quality issues, map manufacturing processes, and understand how adherence to standards like ABNT NBR ISO 9001 can enhance product quality and customer satisfaction.
Challenge
Address recurring customer complaints about missing components and manufacturing inconsistencies in a modern furniture production facility lacking standardized quality controls.
Context
Let's start this activity by thinking about the following question:
How committed are companies to the quality of their products and processes?
Most companies, although they claim the quality of their products, do not always have quality in their processes. Managing quality in a company requires organization, knowledge of processes, and the standards that set the requirements for quality management, in this case, the ABNT NBR ISO 9001 standard.
Imagine the following scenario: A furniture manufacturing company, specialized in tables, chairs, and office cabinets. In the process, the furniture is manufactured by experienced people, with modern technology equipment, and a computerized management system with an MRP structure, among others. However, the company lacks standard operating procedures, process records, and has not established quality indicators for its products and processes. The main problem for this company is the assembly process of the kits, which receives complaints from customers and furniture assembly professionals because pieces are sometimes missing, drilling does not match, the fixing devices do not have a dimensional standard, among other issues.
Source: Prepared by the professor, 2024.
Given the above, how can we ensure the quality of the processes and products of a company like the one mentioned in the example?
What isn't controlled cannot be guaranteed to have the quality that is sold. The greatest asset of a company is its customers. Thus, an unsatisfied customer scores negatively for the company.
Have you ever had the experience of mapping a manufacturing process? If not, you will have the opportunity to exercise this important activity to initiate or maintain the implementation of quality management in a company.
Are you ready? Let's go.
Manufacturing Process Analysis
For this activity, I propose the following steps:
1. Watch the video: "How is furniture produced? Get to know the Kappesberg factory." Available at: Link. Accessed on: Aug 13, 2024.
2. Using quality tools, develop a flowchart of the furniture manufacturing process presented in the video.
Important: When developing the flowchart, point out where, in your opinion, the process stages should be approved or not.
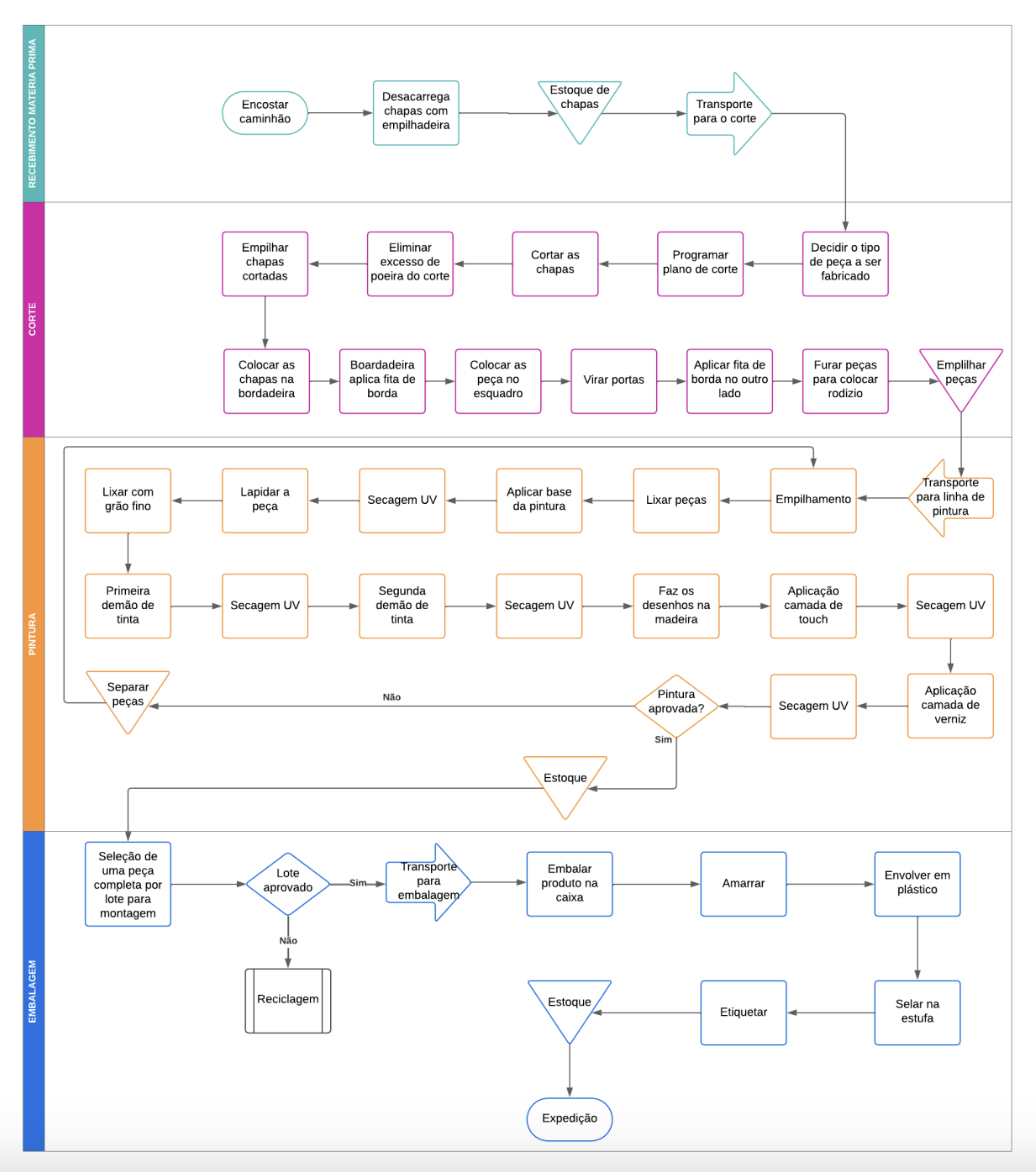
Fig 1. Comprehensive process mapping of furniture manufacturing workflow
3. Based on the video, fill out the following checklist, listing the items to be verified for approval or not of the process stages you consider important to ensure product quality.
Process Stage | Compliant | Non-Compliant |
---|---|---|
Key Process Checkpoints
Process Stage | Compliant | Non Compliant |
---|---|---|
Cutting | ||
Pieces cut according to specifications | ✓ | |
Edges without burrs | ✓ | |
Edge tape applied and well adhered on all sides | ✓ | |
Holes aligned and in the correct position | ✓ | |
Painting | ||
Uniform paint without flaws (scratches, bubbles, stains) | ✓ | |
Pattern of designs and finish as per the project | ✓ | |
Smooth and well-polished pieces | ✓ | |
Clean product with no visible defects | ✓ | |
Assembly | ||
Batch pieces assembled according to plan | ✓ | |
Correct alignment of doors and drawers | ✓ | |
Functional test of doors and drawers | ✓ | |
Handles present, well-fixed, and without imperfections | ✓ | |
Accessories installed according to specifications | ✓ | |
Packaging | ||
Package is tied and sealed | ✓ | |
Label is correct and legible | ✓ |
4. Based on the previous items, answer: In your opinion, what is the importance of process mapping for quality management? Justify your answer in no more than 5 lines.
The mapping of a process is fundamental to providing a clear and structured overview of the entire process. It allows for the identification of the flow of activities, decision points, interactions between stages, and possible redundancies or inefficiencies. This visual representation facilitates communication between teams and serves as a foundation for analysis and improvements in the process.
Strategic Impact Analysis
Process Optimization Results
- 40% reduction in customer complaints
- 25% improvement in production efficiency
- 95% first-pass quality rate